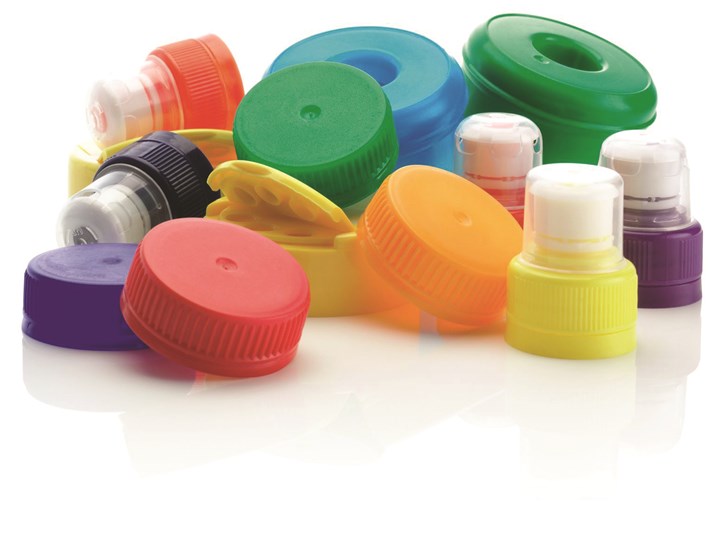
Molded-in color is a bonus of polymer provides. {Photograph}: Avient
When enumerating the advantages of using plastics over totally different provides akin to metals, ceramics, and picket, certainly one of many devices that inevitably comes up is molded-in color. Even in industries like automotive that additionally rely on painting plastics, the long-term objective is to realize the required finish and sturdiness with molded-in color. The plastics commerce has touted this profit for such a really very long time that we repeatedly do not bear in mind the intricacies and potential points that will come up when incorporating color proper right into a polymer. Nonetheless there is a science to this course of; and as with all sciences, there are fundamentals that must be seen if points are to work appropriately. On this text we’ll briefly overview these fundamentals and give attention to the problems that we observe after we fail to stay to them.
Compatibility
There are a selection of key devices that are essential in making a colorant bundle for any polymer. The first of these is the avoidance of any chemical incompatibility between the chemistry of the polymer and the chemistry of the colorant system. Chemical reactions proceed additional rapidly at larger temperatures, and soften processing consists of significantly elevated temperatures and massive inputs of mechanical energy. Subsequently, any chemical interactions which is able to occur between a polymer and a colorant system will happen in a short time all through the injection molding course of.
A whole treatment of the detrimental chemical interactions are too fairly a number of to catalog in an article of this dimension. Nonetheless, a number of examples are worth considering. The literature is filled with papers on the subject of detrimental interactions between PC and TiO2, the primary ingredient in white colorants. Nonetheless, as evaluation progressed it was discovered that TiO2 was not the difficulty. Titanium dioxide simply is not a synthetic; it is a mineral that is pulled out of the underside along with quite a lot of totally different constituents. Amongst these are compounds akin to hydroxides of aluminum and potassium. These are bases and polycarbonate would not do correctly in environments the place bases are present. So take into consideration the implications of exposing polycarbonate to this type of chemical at 600 F (315 C). Degradation will occur rapidly. At current suppliers of white pigments using TiO2 know that the pigment must be dealt with to neutralize these major constituents.
Sometimes the interaction simply is not between the colorant and the underside polymer nonetheless with a minor constituent inside the supplies. When the preliminary efforts to remove heavy metals akin to cadmium and lead from pigments first began inside the early Nineties, the conversion for some provides was pretty seamless whereas in others it was a hard course of. Nylon was an occasion that required a variety of iterations sooner than we obtained it correct. Nonetheless apparently, the preliminary checks on cadmium-free purple colorants with nylon labored pretty correctly. It was not until impact-modified grades of nylon had been tried with the model new pigments that points with ductility turned apparent. The an identical colorant that labored correctly for a general-purpose glass-filled nylon was not applicable for the same supplies formulation with affect modification.
Thermal Stability
The following consideration in deciding on a colorant system is the thermal stability of the colorant system. The colorant chemistry ought to be capable to surviving the temperatures at which the material must be processed. Subsequently, a colorant which can be used for polyethylene or polypropylene, the place processing temperatures will be comparatively low, is also absolutely unsuitable for a cloth akin to polycarbonate or polysulfone, even whether or not it’s acceptable strictly on the thought of chemical compatibility. Going once more to the conversion of purple nylon from cadmium-based to cadmium-free colorants, the preliminary makes an try at producing cadmium-free colorant applications usually resulted in parts that had been lots darker in color than was desired. The color shift was produced by the elevated temperatures and, in some circumstances, by the extreme shear expenses associated to molding large parts with prolonged and complicated transfer paths.
Colorant Amount
Good property retention may also be a function of the amount of colorant that is built-in into the polymer. Colorants are contaminants, nonetheless they’re contaminants that we tolerate on account of they help us get hold of a desired impression. Nonetheless for each combination of polymer and color there is a limit to how lots color will probably be added sooner than the properties of the material are negatively affected. Typically, the first short-term property to exhibit a decline is ductility. Additions of 1-2% of a colorant are usually harmless as long as the chemical compatibility factors talked about above are accounted for.
Nonetheless, as colorant ranges rise the chances are increased that affect effectivity will decline. Sometimes the principle goal of those making a model new color is strictly on aesthetics. Nonetheless in some circumstances attaining a desired color match can include together with comparatively large portions of color to the underside resin, shifting the properties considerably.
For example, I as quickly as labored with a purchaser to develop a white polyetherimide (PEI). Pure PEI is evident nonetheless moreover it’s pretty darkish in color. Making it white can require quite a lot of TiO2. On this case, by the purpose the required look was attained, the TiO2 content material materials was 9%. Nonetheless the patron anticipated the properties to be the an identical as that of the pure resin. If I had been to tell end clients that an unfilled grade of material and a grade that contained 10% of a filler would have the an identical properties, most of them will be justifiably skeptical. Nonetheless no person considered the addition of a comparable amount of an inorganic colorant to be problematic.
Sometimes, the brink ranges are lots lower and are not discovered until one factor goes mistaken. About 10 years prior to now, one in every of my consumers immediately encountered a difficulty with notch sensitivity in a white PC. Toughness was solely lowered noticeably in areas of the half the place sharp corners existed and it gave the impression to be related to a particular lot of material.
This supplies was completely compounded, and the assumption is normally made that formulations are very fixed when a compounder locations the color in versus when it is added as a give attention to the molding machine. Nonetheless in evaluating the pigment loading of quite a lot of raw supplies that produced good parts to 1 that produced brittle parts, we found that the colorant content material materials had elevated from 2% to simply about 4%. This prompted us to hold out some experiments the place we made small samples with pigment loadings that numerous from a low of 1% to a extreme of 4%. We found that the notch sensitivity started showing when the colorant content material materials reached 2.5% and have develop into progressively worse as the amount elevated from there.
There was an fascinating wrinkle to this draw back. In reviewing the compounder’s knowledge we found that their administration over pigment content material materials had in no way been excellent, and however over the course of a extremely prolonged historic previous for the product this draw back with brittle effectivity had in no way been seen. The reason was that the underside PC had modified about 12 months earlier from a V-2 flammability-rated supplies to a V-0 rated supplies. This meant that the model new supplies contained a barely larger focus of a flame retardant. After we repeated the experiment on the notch sensitivity-color loading relationship with the distinctive supplies we found that there was no sensitivity to the amount of color. The properties had been the an identical at 4% as they’d been at 1% and everywhere else in between. This confirmed that it was not as simple as an interaction between the colorant and the polycarbonate. The flame retardant was part of the picture. This components out the importance of considering potential changes ensuing from elements.
Enterprise Modifications
Molecular weight may also be a component that influences the habits of a polymer when positive colors are added. For these of us who’ve been throughout the commerce for a while, we keep in mind the instances when a very powerful supplies suppliers considered the manufacturing of custom-made colors of their resins as an important core competency. I recall visiting an ABS plant operated by Borg-Warner (which subsequently was bought by GE Plastics, which then turned SABIC Revolutionary Plastics, and plenty of others.) The person giving us the plant tour proudly knowledgeable us that they’d practically 40,000 completely totally different colors on file and that of these about 6000 had been energetic. Not solely would they make practically any color you wished, they’d accomplish that at minimal ranges that is perhaps considered ludicrously small by within the current day’s necessities.
Even firms that did not go this deeply into the coloring enterprise nonetheless had 10-12 “commonplace colors” that they’d make in most or all of their base resins. I on a regular basis found it fascinating that in Lexan PC, GE would make every clear and opaque colors of their higher-molecular-weight grades akin to Lexan 101 and 141. Nonetheless they’d solely promote clear colors inside the so-called high-flow grades. The reason was straightforward: Clear colors will probably be made with dyes that are in all probability a lot much less intrusive to the polymer building than pigments. Pigments embody particles, and the size of those particles is crucial to the effectivity of the material. In the event that they’re too small or too large they’ll present a difficulty. The properties of higher-molecular-weight PCs weren’t significantly affected by the opaque colorants, nonetheless the lower-molecular-weight provides had been.
Later, as GE expanded its color decisions, the company eased these restrictions. Nonetheless moreover they began to publish data sheets that made a distinction between the affect energy of the pure supplies and the opaque colored provides. A number of of the data in these data sheets was set off for concern. For example, three grades of base resin with melt-flow expenses of seven, 15, and 25 g/10 min all had notched Izod affect values of 14-16 ft-lb/in. in pure and in clear colors. Nonetheless inside the opaque colors, the Izod affect values for the 7-MFR and 15-MFR provides remained on the an identical ranges whereas the properties for the high-flow grade acquired as a variety. And the range was 2 to 14 ft-lb/in. The exact outcomes trusted which colorant was being added.
Now that the primary supplies suppliers have largely stepped away from the coloring enterprise, the expertise has been taken up by the custom-made compounding neighborhood. It is now their job to focus on these considerations of pigment loading, chemical compatibility, and molecular weight. As will probably be anticipated, this expertise simply is not homogeneously distributed all through the commerce.
Crystallinity
One impression which may be troublesome to anticipate is the have an effect on of a colorant on the best way by means of which crystallinity develops in a semi-crystalline polymer. Many colorants are pure nucleating brokers in a cloth akin to PP. Nucleation changes the crystal building of the material and on the an identical time changes mechanical effectivity, shrinkage, and cycle time. Nucleated provides cycle sooner and shrink decrease than their non-nucleated counterparts. Nonetheless moreover they’re usually a lot much less affect resistant. In case you have got ever had the obligation of molding close-tolerance parts in a variety of colors of a given semi-crystalline polymer akin to PP or acetal (POM), you might need most certainly noticed that you just purchase completely totally different dimensions in a number of colors and may ought to make course of changes to convey the weather once more to print. This is not your creativeness and it is not a case of molding gremlins, it is a manifestation of the best way by means of which constituents inside the colorants change the crystal building of the underside polymer.
Mixing
The best way by means of which the color is built-in into the underside resin may also be important. Completely compounded color is normally hottest on account of it bypasses points with color uniformity that all the time occur when color is added as a minor second ingredient inside the kind of a pellet focus, a dry color, or a liquid. Nonetheless the economics of coloring on the extent the place the half is being manufactured are way more favorable for plenty of causes. These embrace worth per pound, lead events, and the flexibleness to manage inventory and steer clear of pricey obsolescence. If you will purchase 5000 lb of avocado inexperienced ABS, you is perhaps betting on the continued recognition of that color inside the product you make. Sometimes that works out, usually it doesn’t. If the coloring is being completed solely on the extent when the mould is put into the press, the pure supplies simply is not devoted to any specific color until it is time to make parts.
Nonetheless now the color represents a separate ingredient and there are considerations in specification that must be managed. In a color focus, part of the pellet is the colorant and part of it is polymer, a so-called service resin. For most interesting outcomes the service resin must be appropriate with the underside resin into which it is being positioned. Due to this in the event you’re coloring PC the color focus pellets additionally must be product of PC, not PE or EVA copolymer. There’s some latitude. Nylon 66 will probably be colored with a spotlight primarily based totally on nylon 6. Polypropylene and polyethylene are pretty appropriate. SAN will be utilized in a spotlight designed for ABS, nonetheless PS cannot.
Nonetheless proper right here is the important message. There is not a such issue as a typical service. Anyone who has completed polymer mixing is conscious of that only some polymers mix correctly with totally different polymers. Sometimes the calculation is that as a result of the color focus is solely being added at two to 4 parts per hundred the contamination will probably be tolerated. However when the administration over the proper mix ratio simply is not optimum, then the amount of this contaminant moreover fluctuates and points can ensue. Sometimes a significant supplies supplier will current what’s often known as a salt-and-pepper combine—pure pellets and color focus every made by the material supplier and mechanically blended on the best ratio sooner than packaging. It is perhaps good to think about that at least these merchandise are made with relevant consideration to supplies compatibility. Sadly, this is not on a regular basis the case.
In my manufacturing days, we used to make a product in an impact-modified, mineral-filled nylon 66 in every pure and black. The raw supplies was made by a big supplier and they also used a salt-and-pepper mixture for the black. We noticed that whereas the pure supplies ran very correctly, the black parts exhibited quite a lot of magnificence factors and the tactic was very inconsistent on account of the screw had an inclination to slip all through restoration. We lastly analyzed the black focus and positioned that the service resin was EVA copolymer. On the temperatures at which stuffed nylon 66 is processed, EVA begins to decompose and swap to wax, thus creating the problems we had been seeing. After we requested the supplier to interchange the colorant with one primarily based totally on nylon 6, they refused, citing worth. We lastly turned tired of the extreme scrap expenses and glued babysitting of the tactic and began shopping for solely pure. We added our private nylon-based focus purchased from our focus supplier.
Soften Viscosity
The other large mistake that is made with color concentrates has to do with the molecular weight of the service resin. Even when the service is appropriate with the underside resin, usually we uncover that the melt-flow payment of the service resin is eight to 10 events larger than that of the underside supplies. It is believed that that’s required to promote good mixing. Not solely does this apply introduce a low-molecular-weight constituent into the final word half, lowering properties along with the processing window, nonetheless the principle {{that a}} lots lower viscosity for the service resin improves mixing is simply mistaken. Dramatically completely totally different viscosities launched into the molding machine barrel are inclined to segregate considerably than mix.
You’ll perform a straightforward experiment as an illustration this. Take refrigerated mayonnaise and ketchup, which might be generally of comparable viscosities, and mix them in a bowl. Now perform the an identical job nonetheless change the ketchup with tomato juice. You will observe that it takes rather more stirring to evenly incorporate the low-viscosity tomato juice than it does the higher-viscosity ketchup. A small distinction in viscosity is certainly helpful, nonetheless an enormous one simply is not and actually does damage to the final word product.
This is usually a very quick overview of an train that we’re inclined to take with no consideration, incorporating color into our raw provides. There’s lots to contemplate and the self-discipline of coloring, as with most important actions in our commerce, is additional difficult than we predict. So the following time you is perhaps in a enchancment meeting and anyone says they want the product to be blue or purple, put this on the file of issues that must be addressed merely as fastidiously as the rest of the material alternative course of.
ABOUT THE AUTHOR
Mike Sepe is an unbiased, world provides and processing information whose agency, Michael P. Sepe, LLC, depends in Sedona, Ariz. He has larger than 35 years of experience inside the plastics commerce and assists consumers with supplies alternative, designing for manufacturability, course of optimization, troubleshooting, and failure analysis. Contact:
(928) 203-0408 • mike@thematerialanalyst.com.