Instantly, higher than ever, granulation is an important step inside the full manufacturing course of. For lots of processors, significantly these making industrial parts, regrind has sometimes been considered a problem or an important evil. Now, due to the elevated worth of provides blended with elevated requires from purchasers to include reground and/or recycled provides inside the product, utilizing regrind should be thought-about as an enormous promoting various along with a cost-saving method.
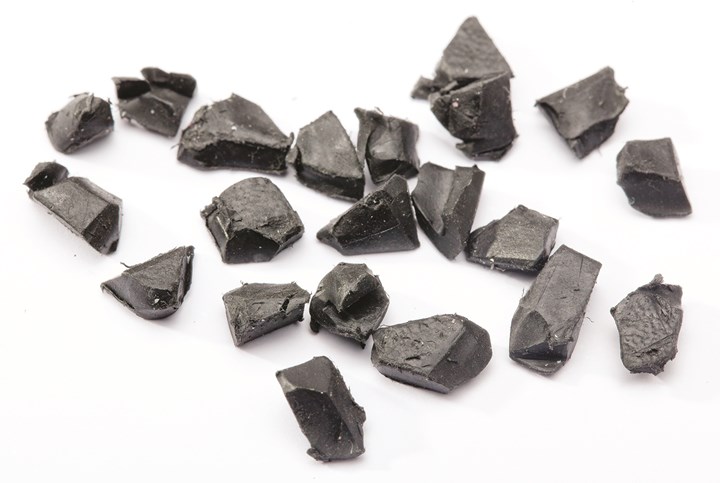
Regrind is taken into consideration good when it is free from mud/fines and of uniform dimension
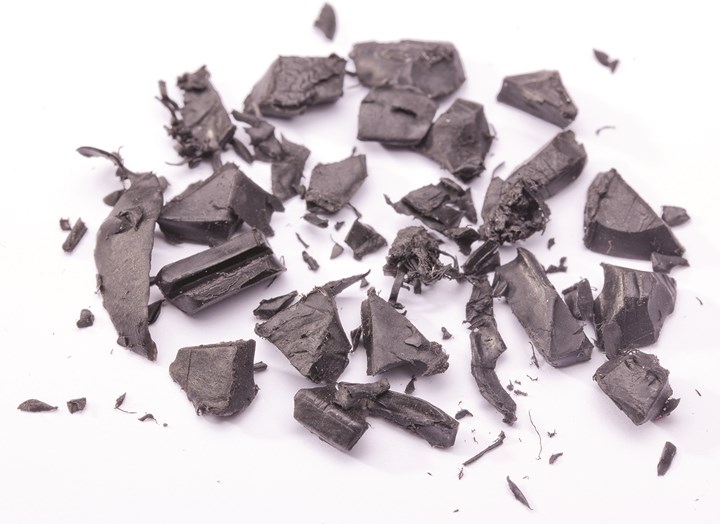
Unhealthy regrind has excessive mud/fines and is non-uniform in dimension.
With the advances in slicing experience and machine design, reductions in energy consumption, and elevated automation on the market for size-reduction methods, there are many cost-effective choices on the market to supply prime quality regrind to the manufacturing course of with out adversely affecting manufacturing costs, half prime quality, or the plant setting. The subsequent are just a few of the quite a few frequent “traps” to stay away from when fascinated about granulation and granulators significantly.
TRAP 1: A GRANULATOR UNSUITED FOR THE TASK
A major lure is to imagine {{that a}} granulator is simply a granulator and that horsepower and throat dimension are all it is worthwhile to know to specify an environment friendly granulation course of. Nothing could very effectively be farther from the truth. Ask any blow molder who has been inside the enterprise for higher than 10 years and you may higher than seemingly uncover that they’ve expert their merchandise “floating” on the rotor. The product bounces spherical inside the slicing chamber for prolonged durations sooner than it is lastly ingested by the rotor. This leads to lower throughputs than anticipated from the tools along with very poor regrind prime quality.
With a goal to decrease supplies successfully, you’ll desire a granulator configured significantly in your utility. If not, rely on elevated energy consumption, excessive mud and noise, lower functionality, and elevated knife placed on. Instantly, most delicate granulator tools suppliers provide modular merchandise that let the builder to configure core machine components to match the actual utility requirements.
You’ll need not lower than seven important gadgets of information to dimension the granulator appropriately:
•Software program or course of: Each course of—blow molding, injection molding, extrusion, recycling—imposes completely totally different requires on a granulator.
•Supplies: Fully totally different provides can react very differently in a granulator.
•Strategy of feeding: Will or not it is handbook, conveyor, robotic, or roll feeding, help head, and lots of others.?
•Half description: A bodily description of the meant parts, equal to bottles, runners, or sheet, is essential to right configuration of the granulator.
•Half dimensions: Try and seize the range of potential half sizes embody largest and smallest, thickest and thinnest.
•Functionality: What lb/hr or kg/hr is anticipated?
•Show display dimension: What final particle dimension do you could reintroduce into your course of?
By way of cautious analysis of the above data, an expert size-reduction expert can be succesful to design and advocate an appropriate reply for what the processor is attempting to realize. This might embody decisions on rotor and cutting-chamber design and the number of mounted knives required. Environment friendly hopper design is perhaps chosen to accommodate the parts and eradicate flyback generated all through granulation.
Together with matching the machine to the making use of, machine builders can be succesful to current the processor with a list of decisions which will help them with working the machine, equal to high-level and high-amp alarms, soundproofing of the hopper and base, and a variety of evacuation and electrical administration decisions.
TRAP 2: A GRANULATOR THAT IS HARD TO MAINTAIN
Repairs of granulators and their important slicing components might be probably the most neglected area of service in numerous vegetation. Repairs is normally delay attributable to time points—that is, the granulator design would not lend itself to the responsibility. Poor or inadequate instruction manuals and lack of supporting choices to simplify options equal to knife servicing make points worse. Lack of maintenance alone may end up in the commonest draw back associated to regrind—poor prime quality granulate with excessive fines and extreme mud content material materials inside the supplies and inside the plant setting.
The two foremost causes for mud and fines are uninteresting and/or improperly gapped knives. The sharper the knives, the additional successfully the granulator will decrease the scrap, significantly with clean, energy-absorbing provides equal to thermoplastic rubber or polyolefin films. Sharper knives produce a cleaner decrease with out pulling and tearing, yielding elevated throughputs, a lot much less mud and fines, a lot much less noise, and higher energy effectivity.
Instantly, most foremost granulator producers perceive that with the rising worth of provides and shrinking maintenance budgets, it’s crucial that granulators be designed for easy cleaning and knife maintenance. Quick and safe entry to the center of the granulator is crucial for optimum productiveness.
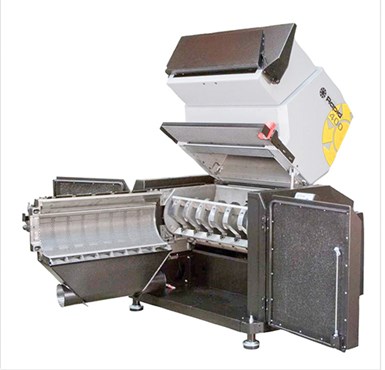
Granulators proper this second are normally designed with maintenance in ideas, offering safe and fast entry to the center of the unit.
Think about a processor working quite a few colors and provides in short-run manufacturing cycles, who needs to clean the machine completely between each run to stay away from contamination. The granulator should be designed to allow the operator to visibly affirm that the machine is evident whereas making sure that the operator is safe when contained within the machine. That is, the granulator should have redundant safety switches for optimum safety and could have choices equal to power-assisted tilt-back hoppers, rotor locking devices, and easily accessible and removable show display cradles and screens. Visibly clear means the operator should have seen paths to all areas of the machine—no hidden nooks and crannies—to look at and make sure the machine is free from all earlier colors or provides which is able to lead to contamination inside the subsequent run.
TRAP 3: A GRANULATOR WITH A POOR KNIFE DESIGN
One different frequent lure is knife positioning and design with little or no scissor-cutting movement, poor rotor design (static rotating knives), non-optimized location of mounted knives, and fewer than optimum rotor knife velocity. All or any of these may end up in non-uniform regrind with extreme mud and fines content material materials and as well as lead to a extreme stage of damage and tear and tear on the granulator.
Always seek for a operate typically often known as “adjustable rotating knives.” These knives are these bolted to the rotor. Along with the mounted knives, they should be saved appropriately gapped and sharpened.
In older granulator designs, these knives are normally mounted to the rotor and thus not adjustable. Since you’re taking away knife supplies everytime you resharpen, the environment friendly rotor diameter can turn into smaller and smaller over the lifetime of the knife. Typically about 10 mm or 3/8 in. of knife supplies can be eradicated over quite a few resharpenings.
With an older machine design, the normal course of is to maneuver the mounted knives forward to compensate for the material flooring off the rotating knives. This results in a reduction of the slicing diameter of the granulator and can enhance the area from the rotating knife methods to the show display. As you moreover decrease supplies in opposition to the show display, this elevated distance between the knife concepts and the show display leads to the “balling” of the material on excessive of the show display, and a for for much longer residence time of the material inside the slicing chamber, producing considerably further mud and fines.
Furthermore, transferring the mounted (mattress) knife forward to compensate for the shortened rotating knives leads to creation of a “shelf” inside the slicing chamber, the place the material can merely assemble up. This shelf impedes the feed into the down stroke of the slicing chamber and results in less-effective slicing.
Pre-adjustable knives and cassette knives are choices found on further fashionable machine designs. Recognizing the importance of knife sharpness and gap, and their relationship to final granulate prime quality, many machine manufactures have standardized on further maintenance-friendly designs for the knives. Pre-adjustable knife fixtures that let the maintenance workers to set the important gap exterior the machine reduce the final downtime of placing in and gapping resharpened knives. Gone are the occasions of sticking feeler gauges into darkish crevices whereas attempting to manage knives inside the machine.
Moreover, on account of the mounted knives are coming proper right into a machined stop inside the slicing chamber, rotating knives can be gapped independently, allowing each rotating knife to have the exact same gap with respect to the mounted knives. That’s unattainable with static (non-adjustable) rotating knives. One different advantage of adjustable rotating knives is the flexibleness to sharpen each knife independently comparatively than collectively as a set. This allows for the minimal amount of material to be flooring off each knife all through each resharpening, resulting in longer whole knife service life.
TRAP 4: A GRANULATOR THAT IS OVER-FED
Many processors seemingly try and destroy their granulator not prolonged after receiving it, inside the establish of “testing the bounds” of what the aptitude of the granulator really is. Your granulator was sized for a particular utility and, hopefully, it is nonetheless utilized in that exact same utility. Nevertheless sometimes when an present granulator is wheeled all through the shop flooring to hold out its duties for a novel half or job, the provides are completely totally different, the throughput is completely totally different…the reality is, the whole thing is completely totally different from what the granulator was initially designed for.
Over-feeding your granulator will clearly once more it up, decreasing productiveness. The decrease in air transfer associated to a completely full slicing chamber leads to less-effective evacuation of the machine. And infeed supplies sits on excessive of the rotor, able to be ingested into the slicing chamber. That supplies, on account of it is utilizing on excessive of the knives and by no means being decrease, is dulling your knives at a earlier than common cost. In some cases of over-feeding, the granulator approaches the utmost amp load functionality of the drive motor and simply jams or ceases working.
Just because it’s greater to remove regrind routinely out of your granulator with an appropriately sized evacuation system, it’s moreover greater to routinely meter-feed your granulator—each with a robotic or a conveyor. Which means, there is not a likelihood of over-feeding your unit.
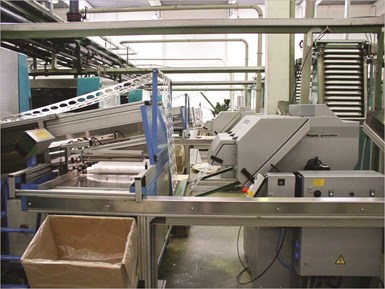
It’s best to routinely meter-feed your granulator—each with a robotic or a conveyer. Confirmed here is a well-designed inline granulation system that features roll-feed and an evacuation system.
There are a variety {of electrical} decisions to help with optimized feeding of the granulator. Extreme-amp alarms can inform you when you end up working the drive motor too exhausting and help the operator understand when to once more off the feed when feeding manually. Extreme-level alarms may assist the operator understand and stay away from evacuation points, as an example if the feed cost is exceeding the evacuation cost it could possibly be as simple as prepared for the evacuation system to catch up. It moreover may save the system from plugging up solely, resulting in most likely pricey harm to the granulator motor.
It’s essential to know the way the granulator is sized for a throughput cost. There’s a big distinction between instantaneous cost and intermittent cost, the latter normally being how the granulator is sized.
Let’s say the granulator is sized for 2000 lb/hr: This normally implies that the machine should be fed at a cost of roughly 33 lb/min (2000 ÷ 60). Do you have to put 100 lb of material inside the hopper in a matter of seconds, don’t rely on the granulator to hold out. This is usually a fairly frequent prevalence with hand-fed granulators.
It is also essential to stay away from under-feeding. In case your granulator sits idle and the rotor spins with out parts inside, the ability effectivity is vastly decreased. You presumably can and can rely on a positive throughput cost out of your granulator, however when your scrap is sitting subsequent to your machine in a gaylord or space for storing, you are undoubtedly not getting most likely probably the most out of your unit.
What inevitably happens is that an over-eager operator dumps your complete subject into the granulator. The consequence: downtime. Frequent, common feeding of your granulator is best for you and for the machine.
No matter their standing as second-class residents, granulators may assist processors be further surroundings pleasant and worthwhile. A major understanding of the traps in granulation and the areas the place granulators need most likely probably the most consideration may make it easier to intend for the acquisition of a granulator or understand the importance of your maintenance schedule to ensure a protracted, productive life in your unit.
ABOUT THE AUTHOR: Kirk Winstead is CEO of the Quick Granulator Group of Bredaryd, Sweden, and is located at Quick Granulator, Inc., in Cranberry Township, Pa. All through his 25 years with Quick, he has labored in a variety of capacities with emphasis on design and product sales of size-reduction gear and methods primarily for the plastics enterprise. Contact: (724) 584-5220; rapidgranulator.com.
Editor’s Phrase: Winstead was with Quick Granulator when this textual content was written. He is now president of and COO Conair Group.