The “general-purpose (GP) screw” can trace its design once more to the Sixties. The thought was to have one screw design in a position to coping with a diffusion of polymers (other than rigid PVC). Once more then, the number of polymers was restricted in distinction with at current and the opponents for manufacturing effectivity was not as good. So the concept made some sense.
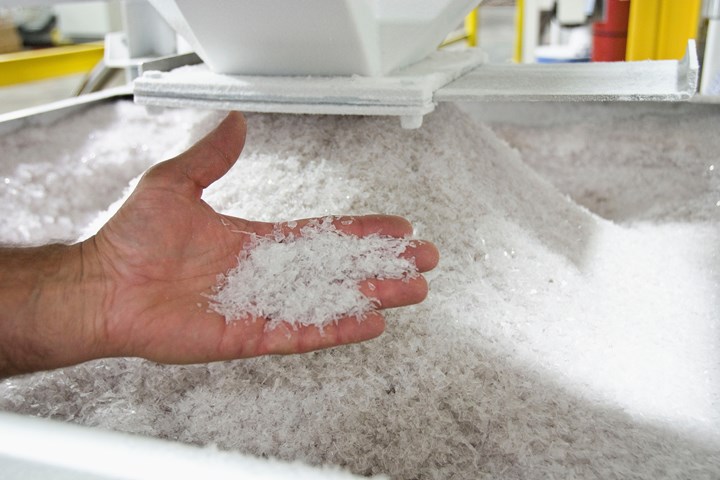
In fact, there’s no such issue as a very “GP” screw, even for recycle extrusion.
With the occasion of additional superior extrusion screw-design know-how and new types of polymers, this concept had largely disappeared. Most processors at current understand the need to have specific screw designs for each polymer to maximise output and soften prime quality. However requests for GP screws are being made additional repeatedly due to the speedy progress in recycling. The demand for clear post-consumer reclaim is strong, and buying a mild present to assist a enterprise requires frequently looking for new sources—besides one has an in-house provide. Usually the recycler processes quite a few major types of polymers and changes quite a few events per week on an extrusion line—subsequently the rise in requests for GP screws.
Nonetheless, there is not a such issue as a “true” GP screw, due to the myriad specific individual polymer traits involved for atmosphere pleasant processing. Throughout the design of a high-productivity screw, the following guidelines reveals some nonetheless not all the data thought-about:
• Viscosity at various shear fees and temperatures;
• Glass-transition temperature;
• Explicit heat and heat of fusion;
• Melting stage and processing temperature;
• Steady, bulk and soften density;
• Feeding traits.
For example, if we consider a sheet-grade HDPE regrind to a sheet-grade PET regrind at equal amount of output (in.³/sec), they require concerning the similar energy enter to attain a typical processing temperature. However, the on a regular basis viscosity for the HDPE inside the screw will be almost double that of the PET. Take into consideration that almost all of the facility enter is completed by shear stress inside the polymer from the rotating screw—not from barrel heating. At equal screw tempo, the resultant energy enter is then largely proportional to the polymer viscosity.
In consequence, the HDPE will soak up 50% additional heat from viscous dissipation than the PET as a result of it passes by way of the screw. If the screw was a very good design for the PET, the HDPE could possibly be correctly beneath its wonderful soften temperature and solely partially melted. If it was a very good design for HDPE the PET could possibly be overheated and doubtless degraded.
Modifications could be made to the working conditions to aim to increased steadiness the facility enter by establishing head stress or reducing the screw tempo. Nonetheless every of these adjustments reduce output—an undesirable consequence. Together with the facility enter, the variations in feeding and melting price would possibly lead to plugging and surging as a result of variations inside the two polymers’ viscosity and frictional traits.
A Increased Strategy
A higher decision is to run the similar form of polymer on an extruder for as long as potential. Usually, pretty broad variations in soften flow into or soften index could also be run on one screw efficiently as long as it’s the similar major polymer. If changeover between polymers is required for the recycle mix, the extruder should be organize with the objects that lower the time to change screws. Such objects are a screw pusher, lifting instruments, quick-disconnect adapter/die, and easily movable downstream instruments such as a result of the pelletizer so there’s home to easily take away the screw. Although many might check out that as time misplaced, the advance in processing price and soften prime quality can merely make up the excellence
Barrier screws are usually a lot much less versatile on a variety of polymer types of recycle than typical single-flighted screws, on account of their major concept is to be designed for a selected melting price and energy enter. Typical single-flighted screws usually have a wider working window, nonetheless it is nonetheless restricted. A straightforward examine is to run the types of recycle frequent to your small enterprise and consider the outputs. One type will always run at bigger outputs, so merely consider the change in output to the time to change screws. When the proper instruments is obtainable, screw changes could also be saved to 1-2 hr, counting on the size of the extruder.
Don’t neglect regarding the purging time when attempting to run utterly completely different polymers on the similar screw. The combination of the misplaced time and wasted polymer alone can equal the price to change screws.
Regarding the Creator: Jim Frankland is a mechanical engineer who has been involved in all types of extrusion processing for higher than 40 years. He is now president of Frankland Plastics Consulting, LLC. Contact jim.frankland@comcast.web or (724) 651-9196.