Proper this second, with all the focus on recycling, some thought ought to be utilized to avoid processing factors when recycling coextruded or co-injection molded parts. Many plastic merchandise are composed of numerous completely totally different polymer layers to provide explicit properties resembling barrier, gloss, coloration, placed on, and so forth. that are very skinny nonetheless must be thought-about when designing screws for recycling. That’s considerably true for semi-crystalline polymers.
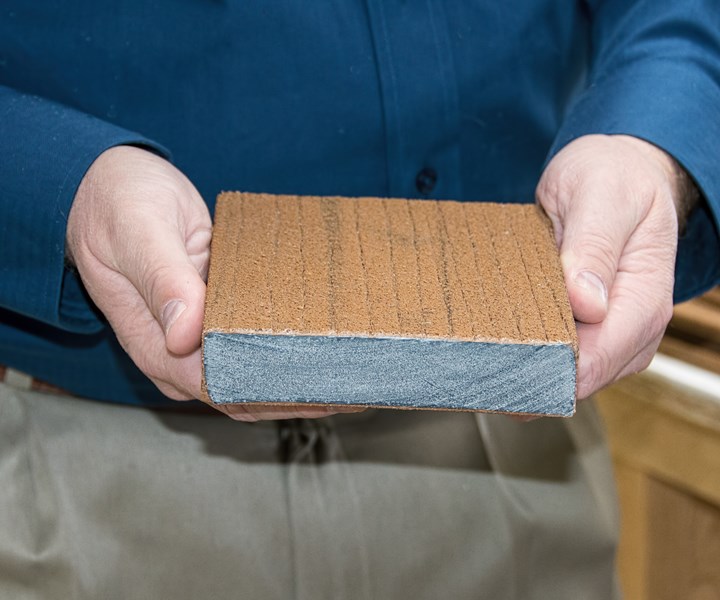
Screw design should be thought-about fastidiously when recycling merchandise composed of combos of provides. (Confirmed proper right here: coextruded deck board with a core layer of mineral-filled post-industrial HDPE and colored HDPE capstock, made by N.E.W. Plastics Corp.)
Semi-crystalline polymers do not soften the least bit until very near their melting stage. As an illustration, let’s ponder a element produced from a semi-crystalline polymer resembling HDPE with an extra semi-crystalline layer resembling PET co-extruded or overmolded. In that case, the HDPE melts at 266 F and the PET at 500 F. As a result of the majority of the recycled article, say higher than 90%, is HDPE, its common processing temperature is usually inside the range of 370-400 F. PET would not even begin to soften—to not point out soften—at that temperature. To someway get the final processing temperature as a lot because the place the PET would possibly moreover soften would degrade or burn the HDPE. The reverse issue moreover applies: If the first polymer had been PET, the required processing temperature would intently degrade the HDPE.
Semi-crystalline polymers do not soften the least bit until very near their melting stage.
There’s a bit a lot much less concern when recycling parts made out of amorphous polymer layers, or combos of amorphous polymers, as they normally soften and transform rubbery properly beneath their typical processing temperatures. Consequently, there may be pretty a disparity between their common processing temperatures and the facility to maneuver them by the use of any tight clearances inside the screw. Their softening stage is called the glass-transition temperature, or Tg. Nonetheless, even with amorphous polymers there is a limit to how far apart the Tg may be for each polymer with the intention to not plug the screw. Semi-crystalline polymers actually have a Tg—they’re known as semi-crystalline because of they embrace a portion of amorphous polymer. Usually, though, it does not affect the circulation to an enormous enough diploma, and they’re usually thought-about not flowable until the melting stage. Due to this fact the melting stage applies to semi-crystalline polymers higher than the Tg for the wants of this dialogue.
In recycling coextruded or co-injected parts having crystalline polymer layers, utilizing barrier screws and shear-type mixers (resembling the quite a few types of Maddock-style mixers) should be fastidiously evaluated. If certainly one of many layers is a semi-crystalline polymer with a so much elevated melting stage than the standard processing temperature of the first polymer, it will be trapped behind the tight clearances of the barrier flight and the mixer lands. The upper-melting semi-crystalline resin will merely not break down and circulation over the barrier flight and or the shear clearances in any mixers. Even a relatively low proportion (decrease than 5%) of the higher-melting polymer will plug the screw, inflicting unstable and decreased output.
For any recycled supplies, along with films, consideration should be paid to the melting and or relative softening components of the half polymers to seek out out whether or not or not the screw design is suitable for that combination of polymers. If there is a thermal incompatibility, then utilizing barrier screws and restrictive mixing devices should be fastidiously evaluated, and the screw design based spherical melting with out such devices. This may normally limit the potential output, so it should enter into the distinctive estimation for profitability of processing recycle. Completely different kinds of screw with out tight clearances will allow the higher-melting or higher-Tg provides to simply transfer by the use of the screw like an inert filler.
ABOUT THE AUTHOR: Jim Frankland is a mechanical engineer who has been involved in all kinds of extrusion processing for higher than 40 years. He is now president of Frankland Plastics Consulting, LLC. Contact jim.frankland@comcast.web or (724) 651-9196.