I get various questions from extrusion processors about whether or not or not they’ll run blended post-consumer reclaim (PCR) their single-screw extruders. With these questions in ideas, proper listed below are some issues it is important consider if this kind of extrusion is part of your plan shifting forward.
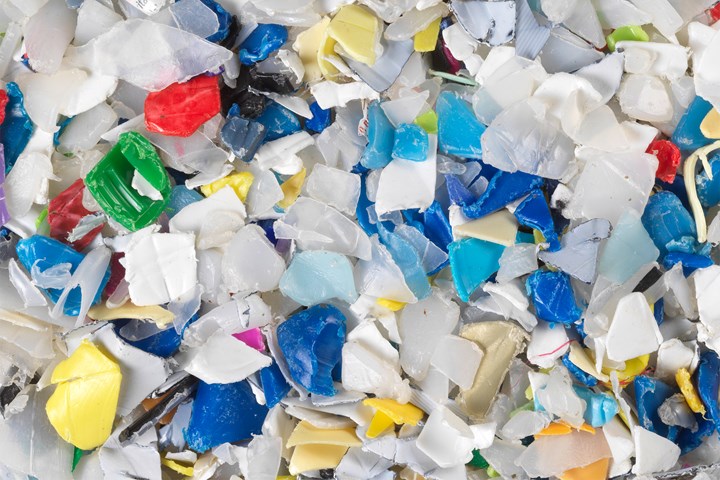
Extruding mixed-plastic waste on a single screw is not any simple matter. Thorough pre-blending sooner than extrusion is necessary, and addition of a mixing half on the extruder might help. Nevertheless the character of the plastics to be blended is likely to be in all probability essentially the most important concern. (Image: Starlinger)
Cleaning Comes First
To start with, the scrap ought to be clear — not merely of steady contaminants, however moreover of oils, lubricants and residual chemical compounds. That talked about, even working completely clear mixed-plastic waste on single-screws has limitations. It’s not like alloying metals. In distinction to metals — whereby mixing completely completely different metals through melting might make alloys that would possibly have substantial effectivity enhancements — many plastics are merely not miscible with one another on account of their molecular building. Often, amorphous polymers is likely to be further merely extruded into workable merchandise than can crystalline polymers, simply because amorphous resins haven’t any crystalline building to dam intermixing. Nonetheless amorphous polymers make up such a small part of the PCR stream that they are comparatively inconsequential to recycling.
To get the best possible outcomes on a single-screw extruder, regardless of the polymers involved, be sure that clear blended scrap is finely flooring and fully blended sooner than feeding it to the extruder. Single screws are nearly continuous-flow devices which have very restricted redistribution performance. In several phrases, the polymer soften would not “slosh spherical” throughout the screw like a fluid. Redistributive mixing is nearly restricted to the amount in a single channel. That signifies that improved mixing ought to be based totally on very small, well-blended particles moving into the extruder. Trying to sidestep these restrictions will vastly limit the potential for single-screw mixing.
Fully completely different Mixes
What about using quite a lot of and aggressive mixing sections to reinforce mixing? Typically, these devices divide the soften into many circulation paths and improve the shear stress on the polymer soften. That can current some “macro” mixing of the various polymers throughout the soften. Nevertheless as soon as extra, many polymers aren’t merely miscible with completely different polymers, and even terribly high-shear mixing cannot energy them collectively.
To get the best possible outcomes on a single-screw extruder, be sure that clear blended scrap is finely flooring and fully blended sooner than feeding it to the extruder.
Moreover, since mixing sections are on a regular basis positioned the place the polymer is often (or completely) melted, their operate is to further divide and shear the mixture. That creates a resistance to circulation, or a stress drop, which reduces the extruder output and raises the soften temperature. No matter that intensive division and shear, a viscous soften has little performance to divide larger particles into smaller gadgets. As a substitute, they merely change their type to maneuver through the mixing gadget because of utilized shear, nonetheless largely keep full measurement.
Making use of shear equally to the mixture of polymers may very well be very troublesome, as they vary immensely in viscosity at comparable temperatures. That means the lower-viscosity portion will get some redistribution and shear stress, nonetheless the higher-viscosity portion will merely “float” alongside throughout the low-viscosity portion. It’s like making an attempt to mix grease in water. Fully completely different polymers at the exact same temperature can vary in viscosity by as loads as 10:1, making incorporation of 1 polymer into one different terribly troublesome even when there’s some compatibility.
Totally different Points
The variations in polymer properties are so broad that a complete host of properties — equivalent to melting degree, density, shrinkage, explicit heat and plenty of mechanical properties — impact the weather of a combination. So it’s troublesome to amass an “alloy” even when it might very effectively be effectively blended.
Any discontinuity throughout the closing mix typically compromises the mechanical properties of the last word extruded half.
All this talked about, many different amorphous polymers is likely to be blended effectively. Even some crystalline polymers is likely to be blended merely because of the similarity of their molecular make-up. For example, LLDPE and HDPE is likely to be blended with out extreme shear to make an alloy with out limiting output. Nevertheless some amorphous polymers equivalent to PVC cannot be blended with most completely different polymers with out excessive lack of properties and degradation and no synergistic enchancment in properties.
The current developments in additive manufacturing have revealed slightly loads regarding the compatibility traits of assorted polymers. A reference to their weldability charts for varied polymers is an efficient begin line to see if the mixture you is likely to be considering has the potential for mixing.
ABOUT THE AUTHOR: Jim Frankland is a mechanical engineer who has been involved in all types of extrusion processing for larger than 50 years. He is now president of Frankland Plastics Consulting LLC. Contact jim.frankland@comcast.web or (724)651-9196.